Piger l’amélioration continue…
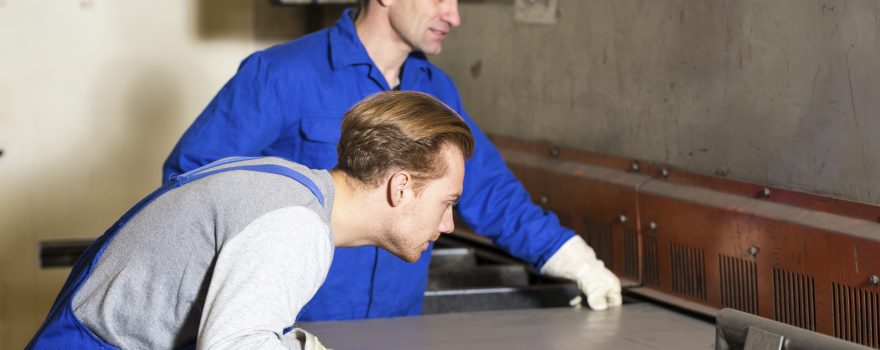
J’ai eu la chance de bénéficier d’un gros investissement dès mon premier poste, dans un atelier de cisaillage organisé en 3×8 et week-end, au sein d’une usine de boîtes métalliques.
La nouvelle ligne était tout automatisée : réglages automatiques des casiers de réception, capacité de la bobine portée à 15t, soit +30%, table de contrôles en ligne, avec des tableaux de rapports sur écran, ce qui était une vraie innovation à cette époque où je n’avais pas encore d’emails.
Le chef de projet m’avait dit avec enthousiasme : « Avec une telle ligne, le temps de changement de format devrait passer de 1 heure à 20 minutes maximum! »
Or au bout de plusieurs semaines, plusieurs mois, le temps de changement de format restait à 55 minutes, 50 minutes les bons jours, parfois remontait à plus d’1 heure. Tous les matins je redoutais le moment de la réunion où je devais montrer les résultats et rendre des comptes. Les questions de mon chef étaient de plus en plus glaciales jour après jour, et mon silence de plus en plus gêné.
Venez voir !
J’ai demandé plusieurs fois aux conducteurs de ligne pourquoi le changement de format était si long. Les réponses variaient entre : « on manque de personnel », « il faut investir dans une nouvelle machine », « c’était mieux avant ». Si j’insistais trop, les réponses pouvaient être plus énervées : « vous n’avez qu’à le faire vous-mêmes ». De fait, j’étais toujours occupé par autre chose au moment où le changement de format se déroulait : une réunion, des tâches administratives, une urgence …
Un jour, un des conducteurs entre dans le bureau et me dit « venez voir ! ». OK. Je le suis vers un ratelier à une certaine distance de la ligne de cisaillage, 15 mètres environ, là où étaient rangées les piges de réglage. Commence alors un échange :
« – Regardez !
– Regarder quoi ?
-Trouvez-moi la bonne pige !
– Je ne sais pas moi, c’est votre métier !
– Justement, avant je les connaissais par cœur, je pouvais les différencier même au toucher. Aujourd’hui, avec la nouvelle ligne, on a de nouvelles piges, mais on en sait plus les différencier. »
Je suis surpris : « Elles sont forcément identifiées, nous sommes ISO quand même !
– Le code est gravé, c’est vrai, mais on le voit mal, d’autant plus que c’est mal éclairé, et les casiers ne sont pas identifiés, donc personne ne les remet à la même place. Ca m’est déjà arrivé de me tromper et de m’en apercevoir après avoir redémarré. En plus à chaque fois il faut faire le trajet depuis la presse, il y a des marches, on court on risque de tomber. »
J’ai pris le marqueur Dymo et fait des étiquettes provisoires sur les piges et les casiers. Le cariste a bougé le casier à piges pour le rapprocher de la ligne. Le lendemain on a procédé à des ajustements en fonction des remarques des autres équipes.
Immédiatement le temps de changement de format a commencé à diminuer. En quelques semaines avec d’autres améliorations de ce type l’objectif était atteint. Et en plus les opérateurs couraient moins pendant les changements de format.
Cette expérience m’a fait « piger » que l’amélioration continue :
- c’est aller voir le problème à l’endroit et pendant le moment où il se déroule
- ce sont des améliorations sur le poste de travail rapides et pas chers avec de grands effets sur la performance.
Et vous, avez-vous connu de telles expériences d’amélioration continue ?